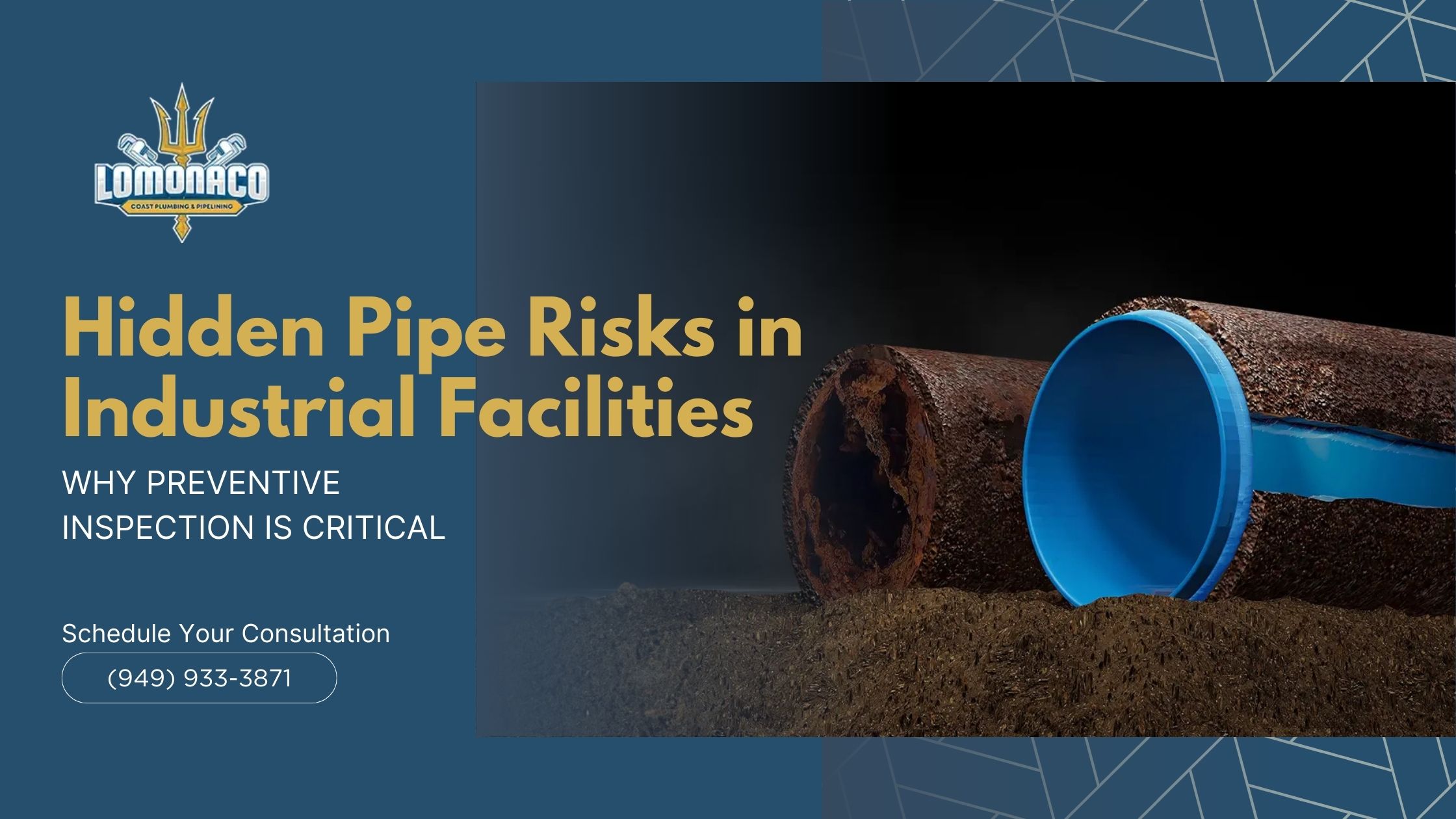
In the world of industrial operations, visible threats receive immediate attention, but it’s often the hidden problems lurking beneath the surface that pose the greatest risk to continuity and safety. Aging plumbing infrastructure represents one of the most overlooked yet potentially devastating threats to industrial facilities today.
The Invisible Threat to Industrial Operations
Industrial facilities face unique plumbing challenges that commercial or residential buildings rarely encounter:
- Chemical exposure: Industrial chemicals accelerate pipe deterioration from the inside out
- Heavy usage patterns: Continuous operations create constant stress on plumbing systems
- Temperature variations: Extreme processing temperatures compromise pipe integrity over time
- Vibration damage: Equipment vibrations gradually weaken pipe connections and supports
- Scale buildup: Mineral deposits restrict flow and increase pressure on aging pipes
What makes these threats particularly dangerous is their invisible progression until catastrophic failure occurs.
Warning Signs Every Facility Manager Should Know
While major pipe failures seem to happen without warning, there are critical indicators that experienced professionals can identify:
1. Decreasing Operational Efficiency
Subtle changes in water pressure, flow rates, or drainage speed often indicate internal pipe restrictions that impact equipment performance long before complete failure.
2. Unexplained Water Costs
Industrial facilities should maintain consistent water usage patterns relative to production. Unexplained increases in water bills frequently signal hidden leaks within concrete slabs or walls.
3. Intermittent Equipment Issues
Production equipment requiring consistent water supply, pressure, or drainage may experience seemingly random performance issues when pipe systems begin to fail.
4. Corrosion at Visible Points
Visible corrosion around pipe access points, valves, or connections typically extends throughout the system, with the worst damage occurring in concealed areas.
5. Facility Age Factors
Facilities constructed before 1980 typically utilized pipe materials with 30-50 year expected lifespans, creating an imminent risk in many of today’s operational industrial buildings.
The Real Costs of Reactive Pipe Management
When industrial pipe systems fail, the consequences extend far beyond repair costs:
- Emergency shutdown losses: Unplanned production stoppages average $50,000-$100,000 per hour in high-volume facilities
- Product contamination: Internal pipe corrosion can introduce contaminants into process water
- Regulatory violations: Leaking industrial pipes may trigger EPA or local environmental penalties
- Worker safety hazards: Catastrophic pipe failures create immediate workplace safety risks
- Insurance implications: Repeated claims for water damage can impact future coverage and rates
According to recent industry studies, nearly 70% of industrial facilities experience at least one significant plumbing emergency every five years, with average remediation costs exceeding $150,000 when accounting for all associated losses.
The CIPP Revolution in Industrial Environments
Traditional pipe repair methods require destructive access, extensive downtime, and substantial restoration. For industrial facilities, this approach is increasingly impractical. CIPP (Cured-In-Place Pipe) technology offers a revolutionary alternative:
Traditional Industrial Pipe Repair:
- Complete production shutdown
- Concrete cutting and removal
- Equipment relocation
- Extensive restoration
- Weeks of disruption
CIPP Technology Advantages:
- Minimal operational disruption
- No excavation required
- Access through existing entry points
- Enhanced chemical resistance
- Scheduled implementation during planned downtime
Case Study: Food Processing Facility
A California food processing facility recently experienced intermittent production delays due to drainage issues. Traditional inspection methods revealed nothing obvious, but our comprehensive camera inspection identified severe internal corrosion and scaling in primary waste lines beneath production equipment.
Traditional replacement would have required:
- 3-week complete shutdown
- Removal of production line equipment
- Concrete floor demolition
- Estimated losses: $1.2 million
Our CIPP solution delivered:
- Weekend implementation during planned downtime
- Zero production disruption
- No equipment relocation
- Complete rehabilitation of 350 feet of compromised piping
- Total project cost: $65,000
The facility avoided approximately $1.1 million in potential losses while extending their infrastructure lifespan by 50+ years.
Implementing a Preventive Pipe Management Strategy
Forward-thinking industrial facility managers are adopting comprehensive pipe management programs:
- Baseline Assessment: Complete camera inspection of all critical plumbing systems
- Digital Documentation: Creating accurate maps and condition reports of hidden infrastructure
- Risk Prioritization: Identifying critical points where failure would cause maximum disruption
- Staged Rehabilitation: Implementing CIPP solutions during scheduled maintenance periods
- Ongoing Monitoring: Regular inspection of high-risk areas to prevent unexpected failures
Don’t wait for catastrophic pipe failure to impact your industrial operation. Our specialized industrial pipe inspection and rehabilitation services provide:
- Comprehensive camera inspection
- Detailed condition assessment reporting
- Rehabilitation planning and scheduling
- CIPP implementation with minimal disruption
- Ongoing monitoring and maintenance programs
Contact Lomonaco Coast Plumbing & Pipelining at (949) 933-3871 to schedule your industrial facility assessment and protect your operation from costly hidden pipe risks.
issues we address
With NuFlow trenchless pipelining solutions, we address the most common problems in residential and commercial sewer lines. This pipe lining process fixes:

advantage of nuflow technology
NuFlow trenchless pipe restoration allows us to repair your pipe with minimal disruption to your daily activities. As we don't have to dig a trench, you won't have to deal with repairing your landscaping, driveway, or sidewalk. NuFlow restoration works on clay, cast iron, concrete, plastic, copper, and steel pipes. The new pulled-in pipe features a lifespan of at least 50 years.
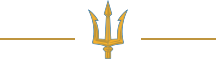
main reasons to work with us
Our team gets the job done right the first time. We update you throughout the project, and we check in afterward to ensure your satisfaction with our work. As a family-owned and operated business, we offer:
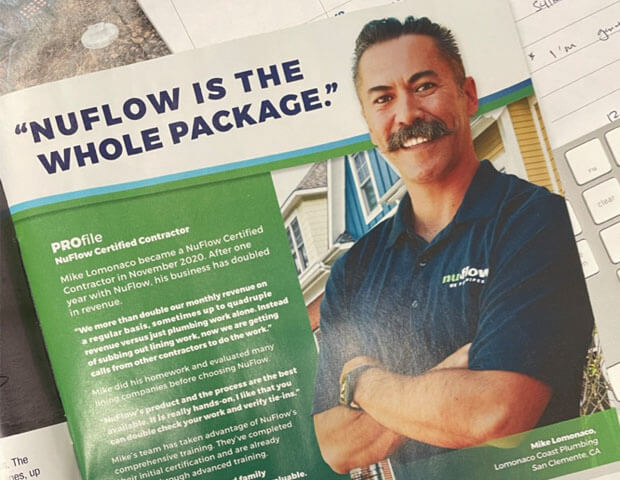
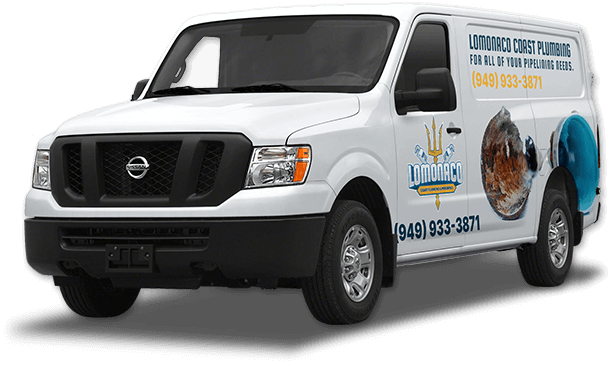
schedule a pipe lining service today
Lomonaco Coast Plumbing & Pipelining proudly serves all home and business owners in the local area. Our on-time arrival and efficient trenchless technology ensure prompt project completion. For more information about NuFlow trenchless pipelining or to schedule an appointment, reach out to our team today.